Table of contents
Single row cylindrical roller bearings with cage
- Bearing design
- Load carrying capacity
- Compensation of angular misalignments
- Lubrication
- Sealing
- Speeds
- Noise
- Temperature range
- Cages
- Internal clearance
- Dimensions, tolerances
- Suffixes
- Structure of bearing designation
- Dimensioning
- Minimum load
- Design of bearing arrangements
- Mounting and dismounting
- Legal notice regarding data freshness
- Further information
Cylindrical roller bearings
Single row cylindrical roller bearings with cage
Single row cylindrical roller bearings with cage are suitable where:
- Bearing arrangements are subjected to very high radial loads ➤ section
- Not only high radial forces but also axial loads from one or both directions must be supported by the bearing position (semi-locating or locating bearing function) ➤ section
- Bearing arrangements must have very high rigidity
- Axial displacements of the shaft relative to the housing must be compensated without constraint in the bearing (in the case of bearings with a non-locating or semi-locating bearing function) ➤ section
- High radial loads and very high speeds occur but the very high radial load carrying capacity of full complement cylindrical roller bearings is not required ➤ section
- The bearings should be separable (one bearing ring can be removed for easier mounting) ➤ section
Cylindrical roller bearing with cage/full complement bearing, comparison of speed and load carrying capacity nG = limiting speed Cr = basic dynamic load rating SL1923 = full complement cylindrical roller bearing NJ23 = cylindrical roller bearing with cage |
![]() |
Bearing design
Design variants
Single row cylindrical roller bearings with cage are available in the basic design as:
- type NU (non-locating bearing) ➤ Figure
- type N (non-locating bearing) ➤ Figure
- type NJ (semi-locating bearing) ➤ Figure
- type NUP (locating bearing) ➤ Figure
- X-life bearings ➤ link
In addition to the bearings described here, Schaeffler supplies single row cylindrical roller bearings with cage in other types, series and dimensions. These products are described in some cases in special publications. If necessary, please contact Schaeffler. Larger catalogue bearings GL 1.
Bearings of basic design – standard range
Key features
Single row cylindrical roller bearings with cage are part of the group of radial roller bearings. In contrast to the ball, the roller has a larger contact area perpendicular to the roller axis. As a result, it can transmit higher forces, has greater rigidity and allows smaller rolling elements under the same load. The single row bearings comprise solid outer rings, inner rings and cages that are fitted with a large number of cylindrical rollers. The rollers have profiled ends, i. e. they have a slight lateral curvature towards the ends. This modified line contact between the raceways and rolling elements prevents damaging edge stresses ➤ Figure. In all standard designs, the cylindrical rollers are guided between rigid ribs by at least one bearing ring. Together with the cage and rollers, this forms a ready-to-fit unit. The other bearing ring can be removed. As a result, the inner ring and outer ring can be mounted separately. Tight fits can thus be achieved on both rings. Bearings of the basic design are manufactured in many different types that differ essentially in the arrangement of the ribs on the inner ring and outer ring. Depending on the design, they are used as non-locating bearings, semi-locating bearings or locating bearings.
Roller profile and stress distribution
|
![]() |
Type NU
Bearings with non-locating bearing function
In bearings of type NU, the outer ring has two rigid ribs, while the inner ring has no ribs ➤ Figure. As a result, axial displacements of the shaft relative to the housing are possible in both directions and within certain limits. During rotational motion, length compensation occurs without constraint in the bearing between the rollers and the raceway without ribs and is therefore practically free from friction. The maximum axial displacement s is given in the product tables. The bearings are used as non-locating bearings, i. e. they cannot guide the shaft axially in either direction ➤ section. For use as semi-locating bearings, they can be combined with the L-section ring HJ ➤ Figure.
Type N
Bearings with non-locating bearing function
Cylindrical roller bearings of type N have two rigid ribs on the inner ring, while the outer ring has no ribs ➤ Figure. Due to the absence of ribs, axial displacements of the shaft relative to the housing are possible in both directions within the bearing. The maximum axial displacement s is given in the product tables. Bearings of type N are used as non-locating bearings, i. e. they cannot guide the shaft axially in either direction ➤ section.
Single row cylindrical roller bearings – Fr = radial load Fa = axial load
|
![]() |
Type NJ
Bearings with semi-locating bearing function
Bearings of type NJ have two rigid ribs on the outer ring and one rigid rib on the inner ring ➤ Figure. In these cylindrical roller bearings, axial displacements of the shaft relative to the housing are possible in one direction only. The maximum axial displacement s is given in the product tables. Bearings of type NJ are used as semi-locating bearings, i. e. they can guide the shaft axially in one direction ➤ section. Semi-locating bearings NJ can be combined with an L-section ring HJ to form a locating bearing unit ➤ Figure.
Type NUP
Bearings with locating bearing function
Cylindrical roller bearings of type NUP have two rigid ribs on the outer ring as well as one rigid rib and one loose rib washer on the inner ring ➤ Figure. In these cylindrical roller bearings, axial displacements between the shaft and the housing are not possible. Bearings of type NUP are used as locating bearings, i. e. they can guide the shaft axially in both directions ➤ section.
Single row cylindrical roller bearings – Fr = radial load Fa = axial load
|
![]() |
L-section rings
Functional expansion by means of L-section rings
In order to expand the function of cylindrical roller bearings NU and NJ, these types can be combined with L-section rings HJ ➤ Figure. In this way, bearings NU can perform a semi-locating bearing function, while bearings NJ in combination with L-section rings can perform a locating bearing function ➤ Figure.
Cylindrical roller bearings NU must not be mounted with two L-section rings, since this can lead to axial bracing of the rollers.
Areas of application of L-section rings
L-section rings can be advantageous where:
- The inner ring in locating bearing arrangements that are subjected to very high loads has a very tight fit; bearings of type NJ + HJ permit tighter fits than bearings NUP, which have a shortened inner ring and a loose rib washer
- The shaft must be axially guided in one or both directions and bearings NJ or NUP are not available
- The design of the bearing arrangement and the mounting and dismounting of the bearings should be simplified
Design of L-section rings
The L-section rings are made from rolling bearing steel and are hardened and ground. The axial runout of the lateral faces corresponds to the normal tolerances of the appropriate bearings. Where available, the L-section rings are listed in the product tables together with the associated bearings (e. g. bearing NJ206-E-TVP2 + L-section ring HJ206-E). Since the L-section rings are not a component of the bearing, these must always be ordered together with the bearing ➤ Figure.
Cylindrical roller bearings with L-section rings – Fr = radial load Fa = axial load
|
![]() |
X-life premium quality
Single row cylindrical roller bearings with cage are supplied up to an outside diameter D = 320 mm as X-life bearings ➤ Figure. These bearings exhibit considerably higher performance than comparable standard cylindrical roller bearings. This is achieved, for example, through the modified internal construction, the optimised contact geometry between the rollers and raceways, the better surface quality ➤ Figure and the optimised roller guidance and lubricant film formation.
Cylindrical roller bearing of X-life design
|
![]() |
Comparison of surface qualities
|
![]() |
Advantages
Increased customer benefits due to X-life
These technical enhancements offer a range of advantages, such as:
- a more favourable load distribution in the bearing and thus a higher dynamic load carrying capacity of the bearings ➤ Figure and ➤ Figure
- a higher fatigue limit load
- lower heat generation in the bearing
- lower lubricant consumption and therefore longer maintenance intervals if relubrication is carried out
- a measurably longer operating life of the bearings
- high operational security
- compact, environmentally-friendly bearing arrangements
Interchangeable with comparable standard bearings
Since X-life cylindrical roller bearings have the same dimensions as the corresponding standard bearings, the latter can be replace without any problems by the higher-performance X-life bearings. The major advantages of X-life can therefore also be used for existing bearing arrangements with standard bearings.
Lower operating costs, higher machine availability
In conclusion, these advantages improve the overall cost-efficiency of the bearing position significantly and thus bring about a sustainable increase in the efficiency of the machine and equipment.
Suffix XL
X-life cylindrical roller bearings include the suffix XL in the designation ➤ section and ➤ link.
Cylindrical roller bearing with cage: Cr = radial basic dynamic load rating
|
![]() |
Areas of application
Due to their special technical features, X-life cylindrical roller bearings are highly suitable, for example, for bearing arrangements in:
- heavy industry (steel production)
- power transmission (gearbox engineering)
- processing machines and construction machinery
- wind turbines (gearbox applications)
X-life indicates a high product performance density and thus a particularly significant benefit to the customer.
Load carrying capacity
Designed for very high radial loads
Depending on the type, single row cylindrical roller bearings can support not only very high radial forces but also high axial loads on one or both sides:
- The types N and NU can only support radial loads. If NU bearings are combined with an L-section ring, these can also support axial loads on one side ➤ Figure
- The type NJ can support radial loads and axial loads on one side. If this type is combined with an L-section ring, it can support axial loads on both sides ➤ Figure
- The type NUP can support radial loads and axial loads on both sides
Higher capacity roller set in variant E
Bearings with the suffix E have a higher capacity roller set and are thus designed for very high load carrying capacity.
Higher axial load carrying capacity of bearings with toroidal crowned roller end face
Neither wear nor fatigue occurs on the rib contact running and roller end faces
In the case of cylindrical roller bearings with toroidal crowned rollers (TB design), the axial load carrying capacity has been significantly improved with the aid of new calculation and manufacturing methods. A special curvature of the roller end faces facilitates optimum contact conditions between the rollers and ribs ➤ Figure. As a result, the axial contact pressures on the rib are significantly minimised and a lubricant film capable of supporting higher loads is formed. Under standard operating conditions, this completely eliminates wear and fatigue at the rib contact running and roller end faces. In addition, the frictional torque is reduced by up to 50%. The bearing temperature during operation is therefore significantly lower. Bearings of the toroidal crowned design are available for a bore diameter of, or larger than, d = 170 mm ➤ link.
Contact geometry of roller end face/rib face –
|
![]() |
Load ratio Fa/Fr
Ratio Fa/Fr ≦ 0,4 or 0,6
The bearings can support axial loads on one side by means of the ribs on the inner and/or outer ring ➤ Figure. In order to ensure problem-free running (tilting of the rollers is prevented), they must always be subjected to radial load at the same time as axial load. The ratio Fa/Fr must not exceed the value 0,4. For bearings with toroidal roller ends (TB design), values up to 0,6 are permissible.
Continuous axial loading without simultaneous radial loading is not permissible.
Permissible axial load
Influencing factors on the axial load carrying capacity
Axial loads are supported by the bearing ribs and the roller end faces ➤ Figure. The axial load carrying capacity of the bearing is therefore essentially dependent on:
- the size of the sliding surfaces between the ribs and the end faces of the rolling elements
- the sliding velocity at the ribs
- the lubrication of the contact surfaces
- tilting of the bearing
- friction
Force flow under axial load – |
![]() |
Calculation of permissible axial load – cylindrical rollers with conventional roller ends
Bearings with standard roller ends
The permissible axial load Fa per can be calculated from the hydrodynamic load carrying capacity of the contact ➤ Equation.
Permissible axial load – bearings of standard design

Legend
Fa per | N |
Permissible continuous axial load. In order to prevent unacceptably high temperatures in the bearing, Fa per must not be exceeded |
Fa max | N |
Maximum continuous axial load in relation to rib fracture. In order to prevent unacceptably high pressures at the contact surfaces, Fa max must not be exceeded |
kS | - |
Factor as a function of lubrication method ➤ Table. The factor takes into consideration the lubrication method used for the bearing. The better the lubrication and in particular the heat dissipation, the higher the permissible axial load |
kB | - |
Factor as a function of bearing series ➤ Table |
dM | mm |
Mean bearing diameter dM = (D + d)/2 ➤ link |
n | min-1 |
Operating speed |
Factor kS
Lubrication method |
Factor kS |
|
---|---|---|
from |
to |
|
Minimal heat dissipation, drip feed oil lubrication, oil mist lubrication, low operating viscosity (ν < 0,5 · ν1) |
7,5 |
10 |
Poor heat dissipation, oil sump lubrication, oil spray lubrication, low oil flow |
10 |
15 |
Good heat dissipation, recirculating oil lubrication (pressurised oil lubrication) |
12 |
18 |
Very good heat dissipation, recirculating oil lubrication with oil cooling, high operating viscosity (ν > 2 · ν1) |
16 |
24 |
The precondition for these kS values is an operating viscosity of the lubricant of at least the reference viscosity ν1 in accordance with DIN ISO 281:2010.
Doped lubricating oils should be used, such as CLP (DIN 51517) and HLP (DIN 51524) of ISO-VG-grades 32 to 460 and ATF oils (DIN 51502) and transmission oils (DIN 51512) of SAE viscosity grades 75W to 140W.
Bearing factor kB
Series |
Factor kB |
---|---|
NJ2..-E, NJ22..-E, NUP2..-E, NUP22..-E |
15 |
NJ3..-E, NJ23..-E, NUP3..-E, NUP23..-E |
20 |
NJ4 |
22 |
Calculation of permissible axial load – cylindrical rollers with toroidal crowned roller ends
Higher axial loads possible
For bearings with toroidal roller ends, the permissible axial loads are 50% higher ➤ Equation.
Permissible axial load – bearings of TB design

Calculation of maximum permissible axial load
For bearings with rollers of the standard or TB design, the maximum permissible axial load Fa max ➤ Equation is calculated from the rib strength and the security against wear. This must not be exceeded, even if Fa per gives higher values ➤ Equation.
Maximum axial load – bearings of standard and TB design

Permissible axial load
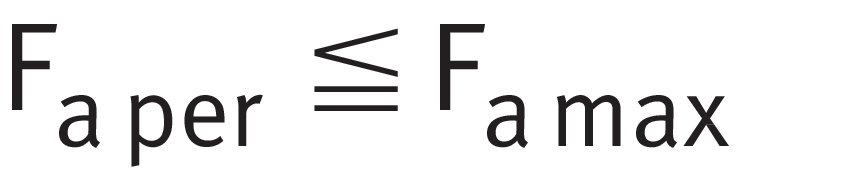
Axial load under shaft deflection
Permissible axial load under shaft deflection of up to 2′
Under considerable shaft deflection, the shaft shoulder presses against the inner ring rib. In combination with the active axial load, this can lead to high alternating loading of the inner ring ribs. Under a shaft deflection of up to 2′, the permissible axial load can be estimated ➤ Equation.
If more severe tilting is present, a separate strength analysis is required. In this case, please contact Schaeffler.
Axial load under misalignment

Legend
Fas | N |
Permissible axial load under misalignment |
Compensation of angular misalignments
Angular deviations are misalignments between the inner and outer ring
The possible misalignment between the inner ring and outer ring is influenced by the internal bearing construction, the operating clearance, the forces acting on the bearing etc. Due to these complex relationships, it is not possible to give generally valid absolute values here. However, misalignments (angular deviations) between the inner ring and outer ring always have an effect on the running noise and the operating life of the bearings.
Permissible tilting
The permissible guide values at which, based on experience, there is no significant reduction in operating life are as follows:
- 4 ′ for series 10, 19, 2, 3, 4
- 3 ′ for series 22, 23
Scope of values
The values apply to:
- bearing arrangements with static misalignment (consistent position of the shaft and housing axis)
- bearings that are not required to perform an axial guidance function
- bearings subjected to small loads (with C0r/P ≧ 5)
Checking by means of the calculation program BEARINX is recommended in all cases. If there is any uncertainty regarding possible misalignment, please consult Schaeffler.
Lubrication
Oil or grease lubrication
Single row cylindrical roller bearings with cage are not greased. They must be lubricated with oil or grease.
Compatibility with plastic cages
When using bearings with plastic cages, compatibility between the lubricant and the cage material must be ensured if synthetic oils, lubricating greases with a synthetic oil base or lubricants containing a high proportion of EP additives are used.
If there is any uncertainty regarding the suitability of the selected lubricant for the application, please consult Schaeffler or the lubricant manufacturer.
Observe oil change intervals
Aged oil and additives in the oil can impair the operating life of plastics at high temperatures. As a result, stipulated oil change intervals must be strictly observed.
Sealing
Providing additional seals in the adjacent construction
The bearings are not sealed; i. e. sealing of the bearing position must be carried out in the adjacent construction. This must reliably prevent:
- moisture and contaminants from entering the bearing
- the egress of lubricant from the bearing
Speeds
Limiting speeds and reference speeds in the product tables
The product tables give two speeds for most bearings:
- the kinematic limiting speed nG
- the thermal speed rating nϑr
Limiting speeds
The limiting speed nG is the kinematically permissible speed of the bearing. Even under favourable mounting and operating conditions, this value should not be exceeded without prior consultation with Schaeffler ➤ link.
Reference speeds
nϑr is used to calculate nϑ
The thermal speed rating nϑr is not an application-oriented speed limit, but is a calculated ancillary value for determining the thermally safe operating speed nϑ ➤ link.
Noise
The Schaeffler Noise Index (SGI) has been developed as a new feature for comparing the noise level of different bearing types and series. As a result, a noise evaluation of rolling bearings can now be carried out for the first time.
Schaeffler Noise Index
The SGI value is based on the maximum permissible noise level of a bearing in accordance with internal standards, which is calculated on the basis of ISO 15242. In order that different bearing types and series can be compared, the SGI value is plotted against the basic static load rating C0.
This permits direct comparisons between bearings with the same load carrying capacity. The upper limit value is given in each of the diagrams. This means that the average noise level of the bearings is lower than illustrated in the diagram.
The Schaeffler Noise Index is an additional performance characteristic in the selection of bearings for noise-sensitive applications. The specific suitability of a bearing for an application in terms of installation space, load carrying capacity or speed limit for example, must be checked independently of this.
Schaeffler Noise Index SGI = Schaeffler Noise Index C0 = basic static load rating |
![]() |
Temperature range
Limiting values
The operating temperature of the bearings is limited by:
- the dimensional stability of the bearing rings and cylindrical rollers
- the cage
- the lubricant
Possible operating temperatures of single row cylindrical roller bearings ➤ Table.
Permissible temperature ranges
Operating temperature |
Single row cylindrical roller bearings |
|
---|---|---|
with polyamide cage PA66 |
with brass or sheet steel cage |
|
|
–30 °C to +120 °C |
–30 °C to +150 °C For continuous operating temperatures higher than +120 °C, please contact us |
In the event of anticipated temperatures which lie outside the stated values, please contact Schaeffler.
Cages
The right cage for any purpose
Standard materials are plastic, brass and steel
Approximately two-thirds of Schaeffler cylindrical roller bearings are supplied with cages. For standard applications, the cage materials used essentially are plastic, brass and sheet steel. A large number of cage types and sizes are designed using these three materials. As a result, the right bearing – in accordance with the operating conditions – is always available. For cylindrical roller bearings standardised in accordance with DIN 5412, there are four standard cages available for selection. A summary of the various cage characteristics and their suitability for certain applications is shown in ➤ Table.
Plastic cage TVP2
The highly versatile plastic cage TVP2 is the standard cage for bearings up to a medium bearing diameter ➤ Table. In comparison with metal cages, it has a range of advantages: low mass, low running noises due to good damping, high elasticity, good tribological characteristics with steel rolling elements and very good emergency running characteristics. This cage is thus a good choice for applications that allow the use of a plastic cage. Due to their wide-ranging positive characteristics, such plastic cages are now in use in many millions of bearings and applications.
Two-piece solid brass cage M1
A classic design of brass cage is the two-piece, riveted-bar brass cage M1 ➤ Table. It comprises a so-called comb cage and a cage cover. The cage parts are joined by means of hot riveting, where the rivet pin is integrated in the cage comb.
One-piece, milled brass cage MPAX/MPBX
The brass cage MPAX or MPBX is intended for demanding conditions, such as the high speeds and radial accelerations occurring in planetary gear bearing arrangements ➤ Table. The optimised pocket geometry and the minimised mass allow a lower running temperature than comparable brass cages. The cages differ in the type of rib guidance. Cage MPAX is guided on the outer ring rib and cage MPBX is guided on the inner ring rib.
Sheet steel cage JP3
For applications that require increased temperature resistance, good lubrication and high geometrical stability of the cage, a bearing with a sheet steel cage is often the most economical solution ➤ Table. With the aid of highly developed manufacturing technologies, the geometry of the crosspieces and thus the running contact of the rollers on the cage bars is significantly improved. This goes hand in hand with a favourable surface structure, which has a positive influence on lubricant film formation.
Cage, cage characteristics, suitability
Criteria |
Cage |
||||
---|---|---|---|---|---|
TVP2 |
M1 |
JP3 |
MPAX |
MPBX |
|
|
|
|
|
|
|
Large number |
+ |
+ |
+ |
+ |
+ |
High radial cage rigidity |
– |
+++ |
+ |
+++ |
+++ |
Low mass |
+++ |
– |
+ |
– |
– |
Good emergency running (damage case) |
– |
+++ |
+ |
+++ |
+++ |
Low noise |
+++ |
+ |
+ |
+ |
+ |
High guidance |
+ |
+ |
+ |
+++ |
+++ |
Strong vibrations |
+ |
+ |
+ |
+++ |
+++ |
Relubrication facility |
– |
– |
+++ |
+ |
+ |
Grease/oil compatibility |
– |
+ |
+++ |
+ |
+ |
Application temperatures > 120 °C |
– |
+ |
+++ |
+ |
+ |
Large temperature fluctuations |
– |
+ |
+++ |
+ |
+ |
Solid cages made from brass and polyamide PA66 are used as standard
Standard cages are shown in ➤ Table. The cage design is dependent on the bearing series and the bore code. Other cage designs are available by agreement. With such cages, however, suitability for high speeds and temperatures as well as the basic load ratings may differ from the values for the bearings with standard cages.
For high continuous temperatures and applications with difficult operating conditions, bearings with brass cages should be used. If there is any uncertainty regarding cage suitability, please consult Schaeffler.
Cage, cage suffix, bore code
Bearing series |
Solid cage |
Solid brass cage |
---|---|---|
TVP2 |
M1 |
|
standard |
standard |
|
Bore code |
||
NU10 |
‒ |
from 05 |
NU19 |
‒ |
from 92 |
NU2..-E, NJ2..-E, NUP2..‑E |
up to 26 |
from 28 |
NU3..-E, NJ3..-E, NUP3..‑E |
up to 28 |
from 30 |
NU4, NJ4 |
‒ |
All |
NU22..-E, NJ22..-E |
up to 26 |
from 28 |
NU23..-E, NJ23..-E |
up to 22 |
from 24 |
N2..-E |
up to 20, 22 to 26 |
21, from 28 |
N3..-E |
up to 16 |
from 17 |
NUP22..-E |
up to 26 |
from 28 |
NUP23..-E |
up to 22 |
from 24 |
Internal clearance
Radial internal clearance
The standard is CN
Cylindrical roller bearings with cage are manufactured as standard with the radial internal clearance CN (normal) ➤ Table. CN is not stated in the designation.
Certain sizes are also available by agreement with the larger internal clearance C3, C4 and C5 ➤ Table.
The values for radial internal clearance correspond to DIN 620-4:2004 (ISO 5753-1:2009) ➤ Table. They are valid for bearings which are free from load and measurement forces (without elastic deformation).
Radial internal clearance of single row cylindrical roller bearings with cage
Nominal |
Radial internal clearance |
||||||||
---|---|---|---|---|---|---|---|---|---|
d |
CN |
C3 |
C4 |
C5 |
|||||
mm |
μm |
μm |
μm |
μm |
|||||
over |
incl. |
min. |
max. |
min. |
max. |
min. |
max. |
min. |
max. |
‒ |
24 |
20 |
45 |
35 |
60 |
50 |
75 |
65 |
90 |
24 |
30 |
20 |
45 |
35 |
60 |
50 |
75 |
70 |
95 |
30 |
40 |
25 |
50 |
45 |
70 |
60 |
85 |
80 |
105 |
40 |
50 |
30 |
60 |
50 |
80 |
70 |
100 |
98 |
125 |
50 |
65 |
40 |
70 |
60 |
90 |
80 |
110 |
110 |
140 |
65 |
80 |
40 |
75 |
65 |
100 |
90 |
125 |
130 |
165 |
80 |
100 |
50 |
85 |
75 |
110 |
105 |
140 |
155 |
190 |
100 |
120 |
50 |
90 |
85 |
125 |
125 |
165 |
180 |
220 |
120 |
140 |
60 |
105 |
100 |
145 |
145 |
190 |
200 |
245 |
140 |
160 |
70 |
120 |
115 |
165 |
165 |
215 |
225 |
275 |
160 |
180 |
75 |
125 |
120 |
170 |
170 |
220 |
250 |
300 |
180 |
200 |
90 |
145 |
140 |
195 |
195 |
250 |
275 |
330 |
200 |
225 |
105 |
165 |
160 |
220 |
220 |
280 |
305 |
365 |
225 |
250 |
110 |
175 |
170 |
235 |
235 |
300 |
330 |
395 |
250 |
280 |
125 |
195 |
190 |
260 |
260 |
330 |
370 |
440 |
280 |
315 |
130 |
205 |
200 |
275 |
275 |
350 |
410 |
485 |
315 |
355 |
145 |
225 |
225 |
305 |
305 |
385 |
455 |
535 |
355 |
400 |
190 |
280 |
280 |
370 |
370 |
460 |
510 |
600 |
400 |
450 |
210 |
310 |
310 |
410 |
410 |
510 |
565 |
665 |
450 |
500 |
220 |
330 |
330 |
440 |
440 |
550 |
625 |
735 |
500 |
560 |
240 |
360 |
360 |
480 |
480 |
600 |
690 |
810 |
560 |
630 |
260 |
380 |
380 |
500 |
500 |
620 |
780 |
900 |
630 |
710 |
285 |
425 |
425 |
565 |
565 |
705 |
865 |
1 005 |
Dimensions, tolerances
Dimension standards
The main dimensions of cylindrical roller bearings correspond to ISO 15:2017 (DIN 616:2000 and DIN 5412-1:2005).
The main dimensions of L-section rings HJ correspond to ISO 246:1995 (DIN 5412-1:2005).
Chamfer dimensions
The limiting dimensions for chamfer dimensions correspond to DIN 620‑6:2004. Overview and limiting values ➤ section. Nominal value of chamfer dimension ➤ link.
Tolerances
The dimensional tolerances of cylindrical roller bearings correspond to the tolerance class Normal, the running tolerance to the tolerance class 6 in accordance with ISO 492:2014. Tolerance values in accordance with ISO 492 ➤ Table.
Suffixes
For a description of the suffixes used in this chapter ➤ Table and medias interchange http://www.schaeffler.de/std/1B69.
Suffixes and corresponding descriptions
Suffix |
Description of suffix |
|
---|---|---|
C3 |
Radial internal clearance C3 (larger than normal) |
Available by agreement |
C4 |
Radial internal clearance C4 (larger than C3) |
Available by agreement |
C5 |
Radial internal clearance C5 (larger than C4) |
Available by agreement |
E |
Increased capacity design |
Standard |
EX |
Increased capacity design, design modified in accordance with standard (parts from these bearings must not be interchanged with parts from bearings of the same size of the previous design E) |
Standard |
JP3 |
Sheet steel window cage, single-piece, roller-guided |
Available by agreement |
J30P |
Black oxide coated (Durotect B) |
Available by agreement |
MPAX |
Solid brass cage, single-piece, rib-guided on outer ring |
Available by agreement |
MPBX |
Solid brass cage, single-piece, rib-guided on inner ring |
Available by agreement |
M1 |
Solid brass cage, two-piece, roller-guided |
Standard |
M1A |
Solid brass cage, two-piece, rib-guided on outer ring |
Available by agreement |
M1B |
Solid brass cage, two-piece, rib-guided on inner ring |
Available by agreement |
TB |
Bearing with increased axial load carrying capacity (toroidal crowned design) |
Standard, dependent on bearing size |
TVP2 |
Solid window cage made from glass fibre reinforced polyamide PA66 |
Standard |
XL |
X-life bearing |
Standard |
Structure of bearing designation
Examples of composition of bearing designation
The designation of bearings follows a set model. Examples ➤ Figure to ➤ Figure. The composition of designations is subject to DIN 623-1 ➤ link.
Single row cylindrical roller bearing with cage – |
![]() |
Single row cylindrical roller bearing with cage – |
![]() |
Single row cylindrical roller bearing with cage, type NJ with L-section ring – |
![]() |
Dimensioning
Equivalent dynamic bearing load
P = Fr under purely radial load of constant magnitude and direction
The basic rating life equation L = (Cr/P)p used in the dimensioning of bearings under dynamic load assumes a load of constant magnitude and direction. In radial bearings, this is a purely radial load Fr. If this condition is met, the bearing load Fr is used in the rating life equation for P (P = Fr).
Cylindrical roller bearings with non-locating bearing function
P = Fr
Non-locating bearings can only support radial loads. For these bearings ➤ Equation.
Equivalent dynamic load
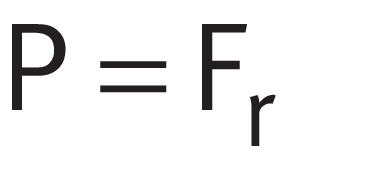
Cylindrical roller bearings with semi-locating or locating bearing function
P is a substitute force for combined load and various load cases
If the condition described above is not met, i. e. if in addition to the radial force Fr, there is also an axial force Fa, a constant radial force must first be determined for the rating life calculation that (in relation to the rating life) represents an equivalent load. This force is known as the equivalent dynamic bearing load P.
Fa/Fr ≦ e or Fa/Fr > e
The calculation of P is dependent on the load ratio Fa/Fr and the calculation factors e and Y ➤ Equation and ➤ Equation.
Equivalent dynamic load
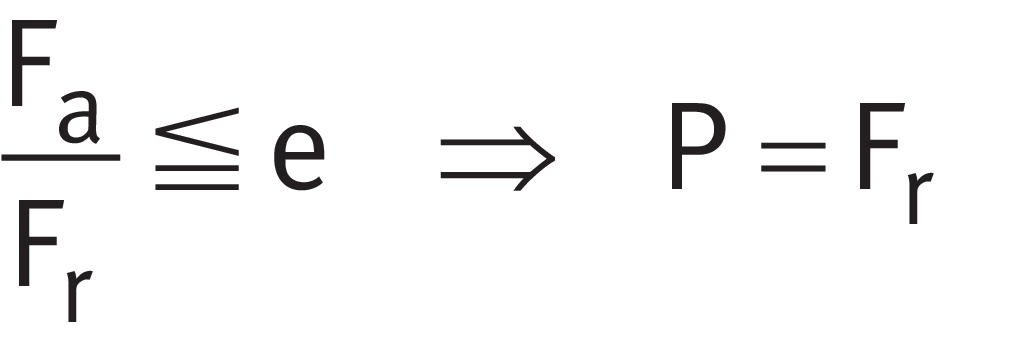
Equivalent dynamic load

Legend
P | N |
Equivalent dynamic bearing load |
Fr | N |
Radial load |
Fa | N |
Axial load |
e, Y | - |
Factors ➤ Table |
Factors e and Y
Bearing series |
Calculation factors |
|
---|---|---|
e |
Y |
|
NJ2, NUP2, NJ3, NUP3, NJ4 |
0,2 |
0,6 |
NJ22, NUP22, NJ23, NUP23 |
0,3 |
0,4 |
Equivalent static bearing load
P0 = F0r
For cylindrical roller bearings subjected to static load ➤ Equation.
Equivalent static load
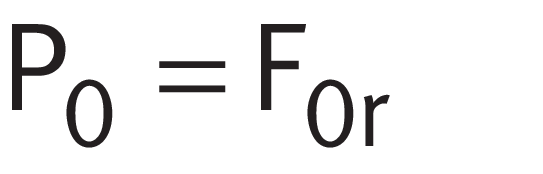
Legend
P0 | N |
Equivalent static bearing load |
F0r | N |
Largest radial load present (maximum load) |
Static load safety factor
S0 = C0/P0
In addition to the basic rating life L (L10h), it is also always necessary to check the static load safety factor S0 ➤ Equation.
Static load safety factor
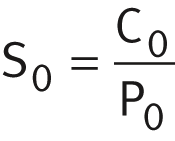
Legend
S0 | - |
Static load safety factor |
C0 | N |
Basic static load rating |
P0 | N |
Equivalent static bearing load |
Minimum load
In order to prevent slippage damage, a minimum radial load of P > C0r/60 is necessary during continuous operation
In order that no slippage occurs between the contact partners, the cylindrical roller bearings must be constantly subjected to a sufficiently high radial load. For continuous operation, experience shows that a minimum radial load of the order of P > C0r/60 is necessary. In most cases, however, the radial load is already higher than the requisite minimum load due to the weight of the supported parts and the external forces.
If the minimum radial load is lower than indicated above, please consult Schaeffler.
Design of bearing arrangements
Support bearing rings over their entire circumference and width
In order to allow full utilisation of the load carrying capacity of the bearings and thus also achieve the requisite rating life, the bearing rings must be rigidly and uniformly supported by means of contact surfaces over their entire circumference and over the entire width of the raceway. Support can be provided by means of a cylindrical seating surface. The seating and contact surfaces should not be interrupted by grooves, holes or other recesses. The accuracy of mating parts must meet specific requirements ➤ Table to ➤ Table.
Radial location
For secure radial location, tight fits are necessary
In addition to supporting the rings adequately, the bearings must also be securely located in a radial direction, to prevent creep of the bearing rings on the mating parts under load. This is generally achieved by means of tight fits between the bearing rings and the mating parts. If the rings are not secured adequately or correctly, this can cause severe damage to the bearings and adjacent machine parts. Influencing factors, such as the conditions of rotation, magnitude of the load, internal clearance, temperature conditions, design of the mating parts and the mounting and dismounting options must be taken into consideration in the selection of fits.
If shock type loads occur, tight fits (transition fit or interference fit) are required to prevent the rings from coming loose at any point. Clearance, transition or interference fits ➤ link.
The following information provided in Technical principles must be taken into consideration in the design of bearing arrangements:
- conditions of rotation ➤ link
- tolerance classes for cylindrical shaft seats (radial bearings) ➤ link
- shaft fits ➤ link
- tolerance classes for bearing seats in housings (radial bearings) ➤ link
- housing fits ➤ link
Axial location
The bearings must also be securely located in an axial direction
As a tight fit alone is not normally sufficient to also locate the bearing rings securely on the shaft and in the housing bore in an axial direction, this must usually be achieved by means of an additional axial location or retention method. The axial location of the bearing rings must be matched to the type of bearing arrangement. Shaft and housing shoulders, housing covers, nuts, spacer rings, retaining rings, adapter and withdrawal sleeves etc. are generally suitable ➤ Figure.
Dimensional, geometrical and running accuracy of cylindrical seats
A minimum of IT6 should be provided for the shaft seat and a minimum of IT7 for the housing seat
The accuracy of the cylindrical bearing seat on the shaft and in the housing should correspond to the accuracy of the bearing used. For cylindrical roller bearings to tolerance class Normal, the shaft seat should correspond to a minimum of standard tolerance grade IT6 and in the housing seat to a minimum of IT7; in the case of tolerance class 6, the shaft seat should correspond to a minimum of IT5 and the housing seat to a minimum of IT6. Guide values for the geometrical and positional tolerances of the bearing seating surfaces ➤ Table, tolerances t1 to t3 in accordance with ➤ Figure. Numerical values for IT grades ➤ Table.
Guide values for the geometrical and positional tolerances of bearing seating surfaces
Bearing |
Bearing seating surface |
Standard tolerance grades to ISO 286-1 |
||||
---|---|---|---|---|---|---|
to ISO 492 |
to DIN 620 |
Diameter tolerance |
Roundness tolerance |
Parallelism tolerance |
Total axial runout tolerance of abutment shoulder |
|
t1 |
t2 |
t3 |
||||
Normal |
PN (P0) |
Shaft |
IT6 (IT5) |
Circumferential load IT4/2 |
Circumferential load IT4/2 |
IT4 |
Shaft | IT6 (IT5) |
Point load IT5/2 |
Point load IT5/2 |
IT4 | ||
Housing |
IT7 (IT6) |
Circumferential load IT5/2 |
Circumferential load IT5/2 |
IT5 |
||
Housing | IT7 (IT6) |
Point load IT6/2 |
Point load IT6/2 |
IT5 | ||
6 |
P6 |
Shaft |
IT5 |
Circumferential load IT3/2 |
Circumferential load IT3/2 |
IT3 |
Shaft | IT5 |
Point load IT4/2 |
Point load IT4/2 |
IT3 | ||
Housing |
IT6 |
Circumferential load IT4/2 |
Circumferential load IT4/2 |
IT4 |
||
Housing | IT6 |
Point load IT5/2 |
Point load IT5/2 |
IT4 |
Numerical values for ISO standard tolerances (IT grades) to ISO 286-1:2010
IT grade |
Nominal dimension in mm |
||||||
---|---|---|---|---|---|---|---|
over |
10 |
18 |
30 |
50 |
80 |
120 |
|
incl. |
18 |
30 |
50 |
80 |
120 |
180 |
|
Values in μm |
|||||||
IT3 |
3 |
4 |
4 |
5 |
6 |
8 |
|
IT4 |
5 |
6 |
7 |
8 |
10 |
12 |
|
IT5 |
8 |
9 |
11 |
13 |
15 |
18 |
|
IT6 |
11 |
13 |
16 |
19 |
22 |
25 |
|
IT7 |
18 |
21 |
25 |
30 |
35 |
40 |
|
continued ▼ |
Numerical values for ISO standard tolerances (IT grades) to ISO 286-1:2010
IT grade |
Nominal dimension in mm |
||||||
---|---|---|---|---|---|---|---|
over |
180 |
250 |
315 |
400 |
500 |
630 |
|
incl. |
250 |
315 |
400 |
500 |
630 |
800 |
|
Values in μm |
|||||||
IT3 |
10 |
12 |
13 |
15 |
16 |
18 |
|
IT4 |
14 |
16 |
18 |
20 |
22 |
25 |
|
IT5 |
20 |
23 |
25 |
27 |
32 |
36 |
|
IT6 |
29 |
32 |
36 |
40 |
44 |
50 |
|
IT7 |
46 |
52 |
57 |
63 |
70 |
80 |
|
continued ▲ |
Roughness of cylindrical bearing seating surfaces
Ra must not be too high
The roughness of the bearing seats must be matched to the tolerance class of the bearings. The mean roughness value Ra must not be too high, in order to maintain the interference loss within limits. The shafts must be ground, while the bores must be precision turned. Guide values as a function of the IT grade of bearing seating surfaces ➤ Table.
Roughness values for cylindrical bearing seating surfaces – guide values
Nominal diameter d (D) |
Recommended mean roughness value Ramax |
||||
---|---|---|---|---|---|
mm |
μm |
||||
Diameter tolerance (IT grade) |
|||||
over |
incl. |
IT7 |
IT6 |
IT5 |
IT4 |
‒ |
80 |
1,6 |
0,8 |
0,4 |
0,2 |
80 |
500 |
1,6 |
1,6 |
0,8 |
0,4 |
500 |
1 250 |
3,21) |
1,6 |
1,6 |
0,8 |
- For the mounting of bearings using the hydraulic method, do not exceed the value Ra = 1,6 μm.
Mounting dimensions for the contact surfaces of bearing rings
The contact surfaces for the rings must be of sufficient height
The mounting dimensions of the shaft and housing shoulders, and spacer rings etc., must ensure that the contact surfaces for the bearing rings are of sufficient height. The transition from the bearing seat to the abutment shoulder must be designed with rounding to DIN 5418:1993 or an undercut to DIN 509:2006. Proven mounting dimensions for the radii and diameters of abutment shoulders are given in the product tables ➤ Figure and ➤ link. These dimensions are limiting dimensions (maximum or minimum dimensions); the actual values should not be higher or lower than specified.
Rib support in axially loaded bearings
Ribs under axial load must be supported over their entire height and entire circumference. The size and axial runout accuracy of the contact surfaces on the inner ring rib must be observed especially in the case of cylindrical roller bearings subjected to high loads, since these factors also influence the uniformity of the rib load and the running accuracy of the shaft. This means that the ribs may be subjected to damaging alternating stresses even in the case of very small misalignments. If the mounting dimensions indicated in the product tables are observed, the problems described can be reliably avoided ➤ link.
Support in semi-locating bearings
In semi-locating bearings, it is sufficient to support the bearing rings on one side, on the rib supporting the axial load ➤ Figure.
Support of the inner ring rib - type NJ(semi-locating bearing) dc = recommended height of shaft shoulder with axially loaded rib Arrow = force flow |
![]() |
Mounting and dismounting
The mounting and dismounting options for cylindrical roller bearings, by thermal, hydraulic or mechanical methods, must be taken into consideration in the design of the bearing position.
Since one bearing ring can be removed, the bearings are easy to mount.
Together with the cage and rollers, the bearing ring with the two rigid ribs forms a ready-to-mount unit. The other bearing ring can be removed. As a result, the bearing parts can be mounted separately from each other ➤ section. This gives simplified mounting of the bearings, especially when the two bearing rings have a tight fit.
Schaeffler Mounting Handbook
Rolling bearings must be handled with great care
Rolling bearings are well-proven precision machine elements for the design of economical and reliable bearing arrangements, which offer high operational security. In order that these products can function correctly and achieve the envisaged operating life without detrimental effect, they must be handled with care.
The Schaeffler Mounting Handbook MH 1 gives comprehensive information about the correct storage, mounting, dismounting and maintenance of rotary rolling bearings http://www.schaeffler.de/std/1B68. It also provides information which should be observed by the designer, in relation to the mounting, dismounting and maintenance of bearings, in the original design of the bearing position. This book is available from Schaeffler on request.
Legal notice regarding data freshness
The further development of products may also result in technical changes to catalogue products
Of central interest to Schaeffler is the further development and optimisation of its products and the satisfaction of its customers. In order that you, as the customer, can keep yourself optimally informed about the progress that is being made here and with regard to the current technical status of the products, we publish any product changes which differ from the printed version in our electronic product catalogue.
We therefore reserve the right to make changes to the data and illustrations in this catalogue. This catalogue reflects the status at the time of printing. More recent publications released by us (as printed or digital media) will automatically precede this catalogue if they involve the same subject. Therefore, please always use our electronic product catalogue to check whether more up-to-date information or modification notices exist for your desired product.
Further information
In addition to the data in this chapter, the following chapters in Technical principles must also be observed in the design of bearing arrangements: